Rotary drilling rig + casing process
Measure and set the line → equipment in place → bury the casing → roll in the casing → grab soil → hoist the steel cage → cast concrete → pull out the casing → set the equipment in place to place a pile
1. Set the pile position of the azimuth drilling rig.
2. Connect the 8m pipe shoe first, and then install it on the azimuth drill. The casing pipe and the pipe shoe are connected with screws, which is convenient for disassembly and assembly.
3. After setting the pile position, use a full-rotation drill to drive the casing for drilling construction. After drilling a casing, a crane can be used to lift another casing, connect it with the casing drilled into the ground, and then continue the drilling operation.
4. In the process of driving casing drilling, if it is difficult to drill the casing, it is necessary to use an impact hammer and impact grab or a rotary drill bit into the middle of the casing to collect soil.
5. Unload the soil.
6. Drive the casing drilling method until the drilling reaches the designed depth, and the drilling work is completed.
7. Lower the steel cage and pour concrete. Put the steel cage in the middle of the casing, and then put it into the grouting pipe. At this point, the concrete is poured. The entire pile hole is filled with concrete as short as possible. If the filling time is too long, it will be difficult to pull out the casing after the concrete has solidified and cause construction accidents. In the process of pouring concrete, the casing can be pulled up to a certain height to prevent the casing from sticking after the concrete has solidified.
Precautions
1. Avoid strong collisions on the casing, especially the joints of the casing. When installing and unloading the connection pins of the casing, it must be cleaned, otherwise it will cause installation difficulties.
2. Drive casing drilling. When the torque increases to the difficulty of driving, it is necessary to use an impact grab or a rotary drill to drill ahead.
3. Check the alignment and verticality of the drill pipe hole before lifting the drill by the rotary bucket to prevent the opening and closing mechanism from hitting the casing shoe when lifting the drill. Open the bottom door under the hole.
4. When grouting the concrete, it is necessary to test whether the various actions of the pipe extruder are normal before starting the concrete grouting.
5. After the grouting is finished, pull out the casing immediately to prevent the floating cage.
Drilling rig introduction
♦ The full-casing full-rotation drilling rig is a new type of drilling rig that integrates full hydraulic power and transmission, electro-hydraulic combined control, and can drive the casing to make a 360-degree rotation. The casing is pressed in and the drilling is performed at the same time, which can solve the piles in complex and special environments. Foundation construction difficulties.
Principle of Drilling Rig
The full-casing full-rotation drilling rig belongs to a kind of Benoyt construction method drilling rig. The specific construction principles are:
Utilize the rotation of the full-pipe full-rotation drilling rig to greatly reduce the friction between the steel casing and the soil layer. While turning it, press it in. At the same time, use the punching bucket and the impact hammer to excavate and take soil until the casing The pipe goes down to the bearing layer at the end of the pile. After the excavation is completed, immediately measure the hole depth to confirm the bearing layer, clear the hole after meeting the requirements, install the steel cage, and pour the concrete to form a pile.
Technical Principle
Typical histogram
Main construction measures
♦ Use disposable casing technology to solve the problem of concrete leakage in karst caves;
♦ Special cutter head, cutter seat and cutter barrel are used to solve the problem of ultra-deep rock;
♦ After entering the limestone, the earth borrowing technique combining impact and grabbing is adopted;
♦ Pile bottom sedimentation adopts gas lift reverse circulation technology to achieve zero sedimentation at the bottom of the pile;
♦ The outer diameter of the steel cage should be less than 10cm of the inner diameter of the casing, and the steel cage should be
A circular precast concrete protection block should be installed every 4m to ensure that the steel cage is in the center of the casing without being hung out by the cutter head or floating up by the pipe strap.
Process flow
Construction operation

Use block stones to backfill and harden the area
within 3m of the upper part of the original collapse area |
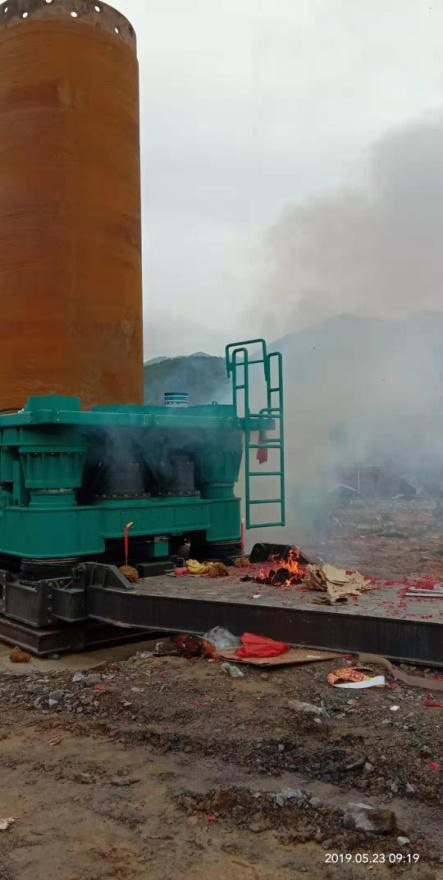
Rig in place
|
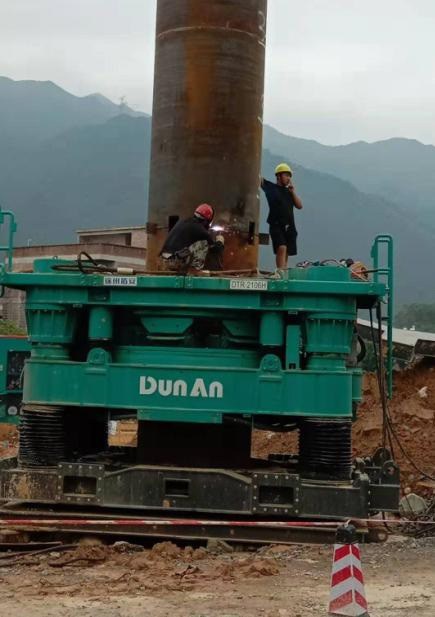
Hole grabbing |
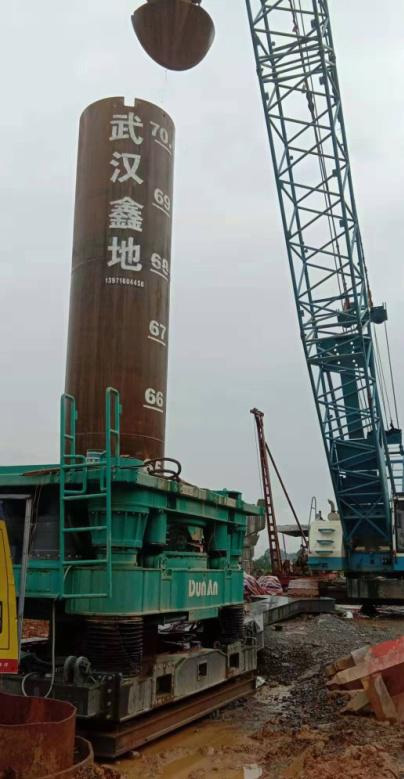
Casing butt |
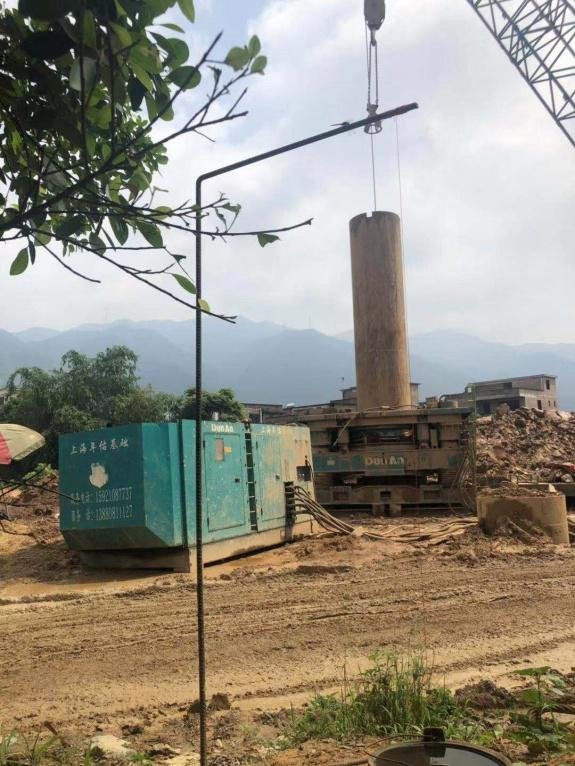
Check verticality
|
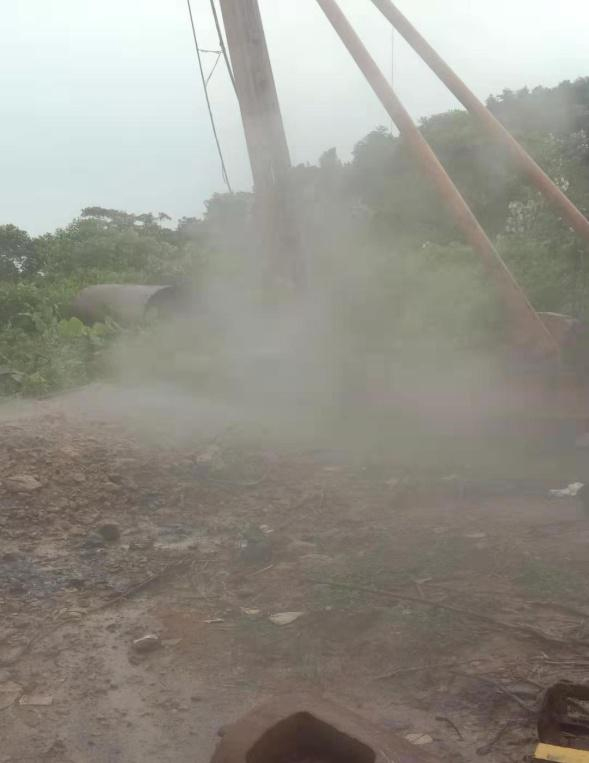
Sleeve cooling protection
(immersion in water) |
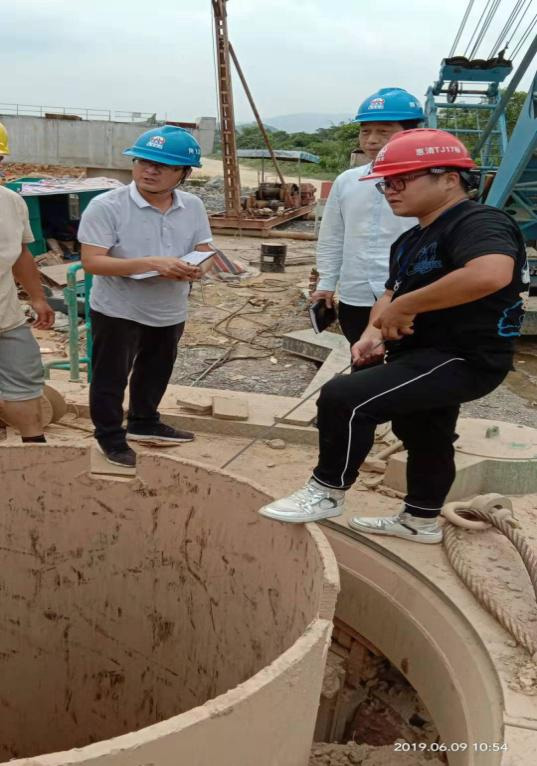
Hole depth acceptance
|
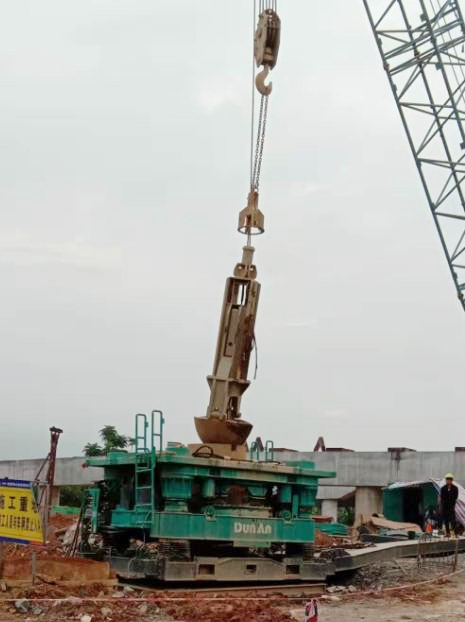
Mechanical cleaning once |
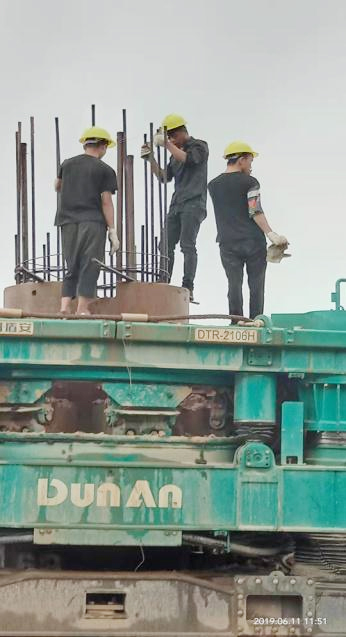
Butt and place the steel cage |
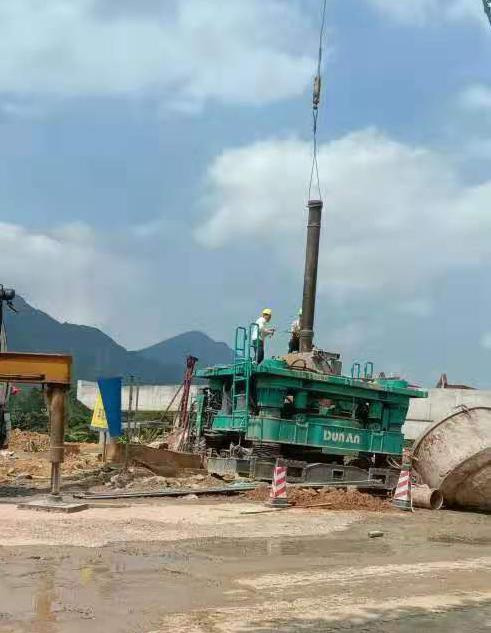
Place the catheter |
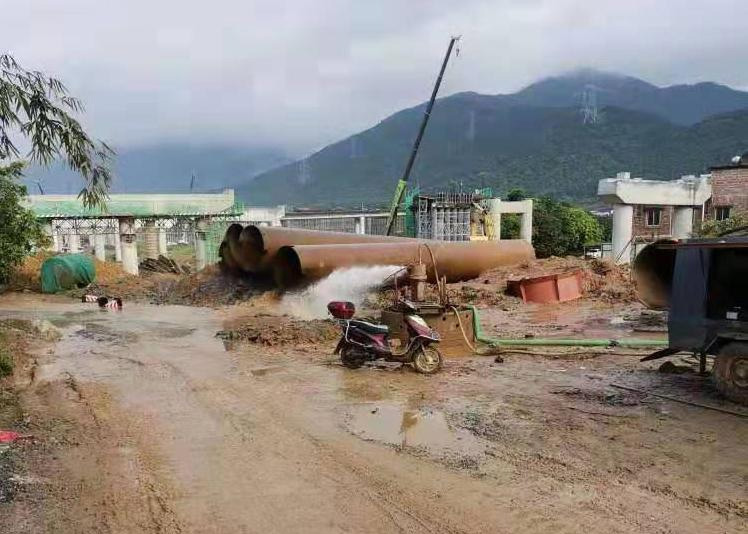
Secondary cleaning |
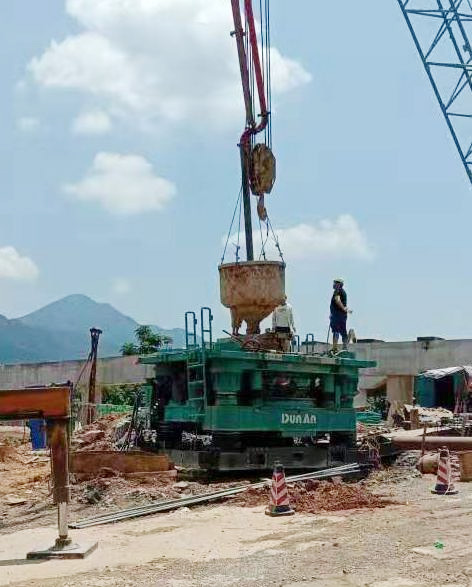
Pouring concrete |